In supply chain and warehouse operations, the process of receiving goods might seem routine at first glance. But it plays a much larger role in keeping things running smoothly. A well-managed goods receipt ensures that deliveries are accurate, inventory records are reliable, and the next steps in the workflow can move forward without delay.
When handled properly, a goods receipt helps teams avoid delays, reduce errors, and maintain strong alignment between procurement, warehouse, and finance. It supports better decision-making and plays a direct role in cost control, compliance, and customer satisfaction.
In this post, we’ll define what a goods receipt is, outline the step-by-step process, and explain why it matters. We’ll also walk through common roles and responsibilities, explore how it differs from an invoice, and offer best practices to help your team improve efficiency and accuracy.
Definition of goods receipt
A goods receipt is the formal confirmation that a business has received a shipment of goods. This process typically takes place at a warehouse, distribution center, or facility when a delivery arrives. At this point, the shipment is inspected and verified against the original purchase order to ensure that the correct items were delivered in the expected quantity and condition.
The goods receipt serves as an official record that materials have been received, counted, and accepted. It also plays a key role in triggering several downstream business processes. These may include inventory updates, quality control checks, and financial activities such as invoice matching and payment authorization.
In many enterprise systems—particularly ERP platforms like SAP—the goods receipt is entered directly into the system. This step updates stock levels in real time and creates a clear audit trail for inventory and procurement teams. Without it, organizations may encounter inventory discrepancies, delayed payments, or gaps in financial reporting that can disrupt the entire procure-to-pay cycle.
Overview of the goods receipt process
While the details of the goods receipt process can vary depending on industry standards and internal workflows, the core steps are generally consistent. A structured process helps teams work efficiently and ensures that all incoming goods are properly verified, recorded, and stored.
Here’s how the typical goods receipt process unfolds:
1. Shipment arrival: The process begins when goods arrive at a receiving location such as a warehouse, distribution center, or plant. Deliveries are usually accompanied by a packing slip or delivery note.
2. Verification against the purchase order (PO): Receiving staff compare the contents of the shipment with the original purchase order. During this step, they check for:
- The correct product
- Quantity ordered versus quantity received
- Any missing, damaged, or defective items
- Proper packaging and accurate labeling
3. Inspection and quality control (if applicable): In certain industries, especially those with strict regulatory requirements, incoming goods must pass a quality inspection before being accepted. This step ensures that products meet internal specifications and compliance standards.
4. Goods receipt entry in the system: Once the delivery is confirmed and verified, the goods receipt is logged in the ERP or warehouse management system (WMS). This system update adjusts inventory levels and creates a digital record of the transaction.
5. Storage or putaway: After documentation, items are placed in their designated storage locations. This may involve using bin numbers, shelf labels, or automated storage and retrieval systems to ensure items are stored efficiently and can be easily located later.
6. Notification to procurement and accounts payable: The completed goods receipt sends a signal to procurement and finance teams, indicating that the order has been received. This step is critical for initiating invoice matching and ensuring timely vendor payment.
Roles and responsibilities in goods receipt
A successful goods receipt process depends on collaboration across several departments. Each team plays a distinct role in making sure goods are received accurately, recorded correctly, and aligned with both procurement and financial workflows.
Key responsibilities include:
- Warehouse/receiving staff: Responsible for physically inspecting and documenting incoming goods.
- Procurement team: Ensures purchase orders are correctly issued and follows up on discrepancies.
- Inventory manager: Updates stock records and monitors availability in real-time.
- Accounts payable: Uses goods receipt data to validate invoices and authorize payments.
- Quality control (QC) teams: Perform additional inspections where required to ensure product integrity and compliance.
Each of these roles contributes to a closed-loop process that connects ordering, receiving, and payment. Strong communication and alignment between teams are essential to keep operations running smoothly and to reduce the risk of delays or errors.
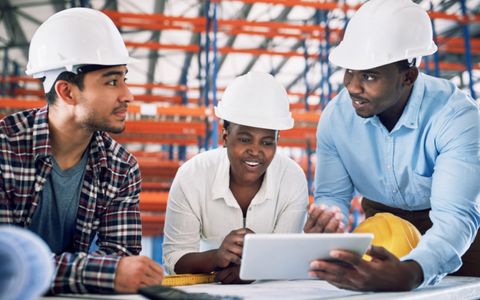
Importance of goods receipt in business
At first glance, the goods receipt process may seem routine. But its impact extends far beyond the warehouse floor. When done well, it helps ensure operational accuracy, financial accountability, and regulatory compliance across the organization. Below are some of the key reasons this process matters.
Ensuring accurate inventory tracking
One of the most immediate benefits of a well-managed goods receipt process is inventory accuracy. When incoming items are verified and recorded promptly, stock levels reflect what’s actually on hand. This helps reduce stockouts, avoid overstocking, and support better forecasting.
Accurate inventory is especially important in just-in-time (JIT) manufacturing environments, where even small delays or errors can disrupt production schedules. In retail and distribution, precise receiving helps businesses meet demand efficiently while minimizing excess inventory and storage costs.
Financial implications of goods receipt
The goods receipt process also plays a critical role in financial control. It initiates what’s known as the three-way match, which compares the purchase order, the vendor invoice, and the goods receipt to ensure all records align. This step helps prevent overpayment, duplicate payments, or payment for goods that were never delivered.
From a broader financial perspective, goods receipt data contributes to more accurate budgeting, spend analysis, and financial reporting. It also strengthens audit trails by ensuring that the value of received goods is recorded in the correct period and tied to a verified transaction.
Compliance and quality assurance
For businesses operating in highly regulated industries—such as life sciences, aerospace, or food and beverage—goods receipt is a key part of maintaining compliance and quality control. The documentation it provides helps meet internal audit requirements and external regulatory standards.
Incorporating quality checks into the receipt process also allows teams to catch defects early. This reduces the risk of faulty goods entering production or reaching customers and supports stronger supplier relationships by documenting recurring issues. Over time, this helps build a more reliable and accountable supply base.
Key differences: goods receipt vs. invoice
Although closely connected in the procure-to-pay process, a goods receipt and an invoice serve very different functions and involve separate teams.
A goods receipt is an internal record that confirms a shipment has been delivered, inspected, and accepted. This step is triggered by the physical arrival of the goods and is typically managed by the warehouse or receiving staff. The purpose is to verify that the correct items were received in the right quantity and condition. Once the verification is complete, the goods receipt is entered into the system to update inventory, initiate any required quality checks, and confirm that the purchase order has been fulfilled.
An invoice, by contrast, is a financial document submitted by the vendor to request payment for the goods or services provided. It is usually triggered after the shipment is made or the service is completed. Invoices are handled by the accounts payable team and are used to reconcile financial records and process payments.
In short, the goods receipt confirms what was physically received, while the invoice represents the supplier’s request for payment. For an accurate and compliant transaction, these two documents—along with the original purchase order—must align as part of the three-way match process. This alignment helps ensure financial control and prevents errors in payment.
Best practices for goods receipt management
Improving the goods receipt process starts with having clear procedures, well-trained staff, and the right digital tools. When these elements work together, businesses can reduce errors, speed up workflows, and create more consistent operations across locations.
Here are several best practices to strengthen your approach:
- Use digital systems for receipt entry: Manual paperwork is prone to delays and errors. Leverage ERP systems, mobile apps, or barcode scanners to capture receipt data in real time.
- Standardize receiving procedures: Develop clear checklists or SOPs (standard operating procedures) for all incoming shipments to ensure consistency across teams and sites.
- Train staff regularly: Ensure warehouse and receiving personnel understand how to verify deliveries and enter receipts accurately.
- Incorporate quality control where necessary: Build in quality inspection steps as appropriate, particularly for critical or regulated items.
- Integrate with procurement and finance: Seamless data sharing across departments enables quicker resolution of discrepancies and faster payment cycles.
- Track KPIs related to receiving: Monitor metrics like receipt accuracy, turnaround time, and discrepancy rates to identify areas for improvement.
Making goods receipt work for your business
For organizations looking to improve inventory and procurement performance, getting the goods receipt process right is essential. It’s more than just recording deliveries. It’s about building a dependable system that supports inventory accuracy, enhances financial control, and strengthens supplier relationships.
When teams understand the process, receive consistent training, and use the right digital tools, they’re better prepared to handle incoming shipments with speed and precision. This clarity reduces costly errors, minimizes delays, and keeps operations aligned from the warehouse floor to financial reporting.
Whether you're managing day-to-day warehouse operations or driving procurement strategy, refining your goods receipt process helps lay the groundwork for long-term supply chain success.
Ready to strengthen your goods receipt process?
With the right tools in place, your team can streamline receiving, improve inventory accuracy, and reduce costly errors. Prometheus Group offers integrated, user-friendly solutions that connect your goods receipt workflows with the rest of your supply chain operations.
Contact Prometheus Group today to learn how our platform can help you optimize inventory, simplify receiving, and drive better results across your business.