IBM Maximo is not for the faint of heart. And neither is working in Maintenance Planning and Scheduling, if we’re being honest. Whether you work in Utilities, Oil and Gas, Facilities Management, at an airport or a port, or anywhere in between, choosing the right Planning and Scheduling tools for Maximo is bound to be a big decision.
So, we went to the AKWIRE insiders: some of the folks from technical support, client services, and training to get their take on FAQs, best practices, quick fixes and everything you’ve ever wanted to know about AKWIRE (now part of Prometheus Planning & Scheduling).
But... we did it mad-libs style.
Enjoy!
Question 1: Everyone asks me if AKWIRE can…
Richard: I often hear the question, “Can AKWIRE show Craft Requirements at the Parent, Child and Task WO levels?” The answer is absolutely, yes. Craft Requirements and Assignment can be displayed at any level of a WO as long as that level of work order is brought into your schedule from Maximo. And once we’ve said that, their next question is almost always, “Can you reschedule those items independently of one another?” And again, the answer is yes. Each Parent, Child or Task work order can be scheduled independently of the others.
Janna: Another thing that many Maintenance Schedulers want to know is, “Can AKWIRE show me all the WOs assigned to a single person?” They light up when I show them how easy it is to filter down the data to show the WOs assigned to one individual in the Labor Heatmap.
Elliot: Many people will ask me about user defined fields that are unique to their business. They want to know if AKWIRE can update those fields on the work orders. To which I say, “easy peasy!” In case that wasn’t clear, that’s a yes.
Shannon: Right up there with some of my most frequently asked questions about AKWIREis “How do you manage Availability exceptions?” In AKWIRE, you can manage all type of Availability exceptions from vacation, training and partial or full days to maternity/paternity leave, bereavement and more. You can configure AKWIRE to have all the Availability exceptions you need, plus you can now also manage Asset and Location availability there too.
Duong: Everybody wants to know if they can write mass changes back to Maximo. The answer is yes: AKWIRE can do that in just a couple of clicks. Yes, you can change the status of a Work Order in AKWIRE. Yes, you can edit your data directly in AKWIRE and yes, those changes will publish to Maximo!
Question 2: I see this happen on so many implementations/training sessions…
Shannon: AKWIRE was built to be user-friendly and easy to understand, but Planning and Scheduling is complex work, and learning a new software takes practice. Hands down, the clients who master AKWIRE the fastest are the ones who love practicing in a test environment. That way, they can practice worry-free. And when they can play around in the tool, they discover all the neat shortcuts and cool features that they can use to make their work go faster and easier.
Elliot: People get blown away by what they can now see that they could not before. Users start with two or three schedules. A year into the process, it’s like night and day. They have 20 schedules to meet really precise scheduling or reporting processes. You see how people grow (in their use of the application) right in front of your eyes. Suddenly, the shy person in the room is the expert helping everybody out. It’s awesome to watch people blossom.
Richard: Prior to using AKWIRE, many people fall into one of three camps: 1) They’ve got solutions that don’t work. 2) They don't have any Planning and Scheduling solutions. 3) They’ve had a “solution” that disappointed them, so they went back to doings things the old way, in Excel. I can’t tell you how many times I’ve heard the comment, “This is SO much easier than how we were doing it before!”
Janna: When you go to a client’s site to do training, you never know the full story of what they’ve been through. You don’t always know what they’ve used in the past, and what’s brought them to this point. Sometimes, I’ll arrive at a client’s site and there are some skeptics in the room. They’ve been burned before. They’ve been promised the tools will work. They’ve been told the tool had features, but then discovered those features won’t be out “until the next release”. So, I see people who are expecting to be let down. It is so satisfying to watch their expressions change when they see with their own eyes how fast and easy it is to do their work. When they see the filtering and grouping, the one-click scheduling, the heatmaps change color… when they see AKWIRE in action, they become believers.
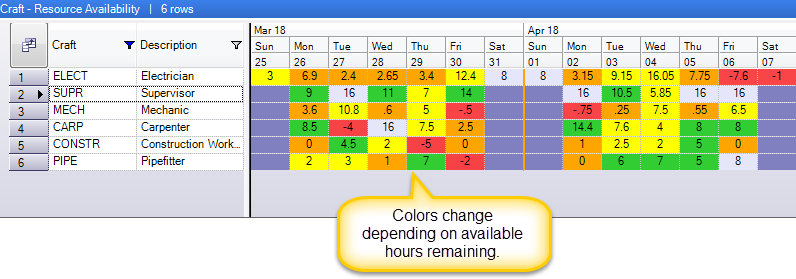
Question 3: Some configurations are more popular than others. These are the ones I see the most…
Elliot: By far, it’s color coding. I see many clients who want to define certain properties for their work orders that will make those rows display in a specific color. Often that color is red.
Duong: Every client with whom I’ve worked wants to create a layout or layouts with the colors, styles, and fonts specific to their working style or organization. Setting this up makes it easy for them to see the information they need at a glance.
Richard: So many! For configurations, we see a lot of folks who want to add calculated columns, bring in columns from other objects (e.g. Asset, Location), and conditionally bring in WOs. In terms of layouts, since users can create their own, this varies quite a bit. But some of the most popular variances I see are: Date formats (e.g. Year-Month-Day, Day-Month-Year, Month-Day-Year, etc.), font size, making certain columns a different color so they stand out (e.g. Sched Start and/or Sched Finish), Required Crafts, Assigned Labor, etc. The list goes on.
Question 4: If I had a dime for every time I saw these problems with a client’s Maximo data…
Elliot: The problems with Maximo data can vary significantly. But it’s those problems coming to light that can cause the most heartburn initially. During an implementation of AKWIRE, clients “suddenly” get full visibility of their Maximo data. And all at once, they can see hundreds of bad data records. It can be overwhelming for a second – but then they realize that now that they’ve spotted the bad data, it’s easy to fix it in bulk. They realize they might never have found all those bad records if it was not by using a tool that provides so much visibility.
Shannon: This is a BIG one! Bad or old data is visible more than ever to our customers as we pull their data from Maximo into AKWIRE… you begin to hear the customer say things like, “We don’t even go to that location any more”, or “That asset isn’t even in service or it’s been replaced”, or “That person/supervisor isn’t on the contract any longer”. AKWIRE has the powerful capability to showcase the customers’ data in such a way that provides a “light bulb” moment.
Richard: Some data problems crop up more often than others. A few I see often are: incorrect statuses on the Person and Labor records (e.g. Active versus Inactive). We also see a lot of Labor records that have the wrong default craft. In general, we encounter a lot of outdated WOs in the backlog (e.g. Supervisor, lead, no craft requirements). Thankfully, AKWIRE helps Planners and Schedulers spot these errors and fix them in bulk, quickly.
Question 5: Here’s an “issue” that can be fixed in a snap…
Elliot: Often, users want to query precise and seemingly complex WO criteria, not just from the WO data, but also from other tables and columns that are not part of the WO table, including custom tables. In other solutions, you’d have to be a SQL whiz to achieve this, but with AKWIRE, it’s quite do-able, even for a user with little SQL experience. We can make it as simple as picking from a dropdown. I’m not kidding. It actually can be that easy.
Richard: I see issues arise on occasion where there’s a difference in the “philosophy” of what “assigning” means. For instance, you may have some users populating a WorkOrder.Lead versus others populating the Assignment.LaborCode. Utilizing our Labor heatmap with our standard configuration requires the Assignment.LaborCode be populated. Ensuring everyone is using the same terminology ensures expectations are met and exceeded.
Duong: After downloading DLLs or Zip files from the internet, users may see the message “Could not load file or assembly file”. Luckily, this is easy to fix.
The most likely cause of the issue is that Windows has blocked the files. You simply need to right click on the file(s) to bring up their Properties dialog. If the file is blocked, you’ll see an Unblock option. Tick the checkbox and click OK.
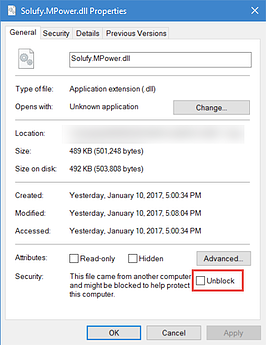
And don’t forget, it may be easier to unblock the zip file before extracting. That way, you won’t have to unblock all the individual files contained within the zip file.
Question 6: If I could only say one thing to someone who is thinking about choosing AKWIRE, it would be…
Elliot: One time, I was asked, “Why does AKWIRE have so many options?” and the perfectly analogy came to mind. This tool gives you flexibility to do business how you need to do business. If the options were not there, you would have to change your business process to match our vision. So, think of it this way: AKWIRE is not a train on tracks, but more like a dirt bike that can go anywhere.
Richard: We get asked a lot, “Is there anything AKWIRE can’t do?!” In fact, many clients are so impressed by the configurability and number of features in AKWIRE, they almost make it a goal to find something AKWIRE can’t do. We always welcome that challenge. Bring it on. 😉
Duong: If there’s just one thing you need to know, it’s like AKWIRE makes things easier to manage. Its user-friendly UI helps Planners and Schedulers manipulate their data in a way that’s effective for them, which means they can make more effective scheduling decisions and get more done in less time.