Everyone likes to have autonomy and choice as part of their work day. It’s human nature, I think. But, just like we are all beholden to the tasks we must complete, the goals we want to accomplish, and the responsibilities of our roles, sometimes what we have to do isn’t necessarily what we’d like to do.
And that’s just the reality of working.
In my years as Maintenance Scheduler at the Kennedy Space Center, and now when I visit clients as a Trainer, I continue to see organizations struggling with maintenance technicians choosing unscheduled work orders rather than following the schedule.
Why does this happen and why is it a problem? Here’s my two cents.
Picking and choosing printed maintenance work orders
If you’ve Planned or Scheduled at more than one organization, then you’ll know that every business does it differently. The processes, tools, resources, and company culture all influence how Planning and Scheduling is done. Some might have state-of-the-art software tools and some might still be plugging away on Excel.
But in many cases I’ve seen, whether they’re using the newest technology or not, an old habit lingers – and that’s maintenance technicians choosing unscheduled work orders rather than tackling the work orders that have been scheduled for that day or week.
It often happens when the work orders are printed out and distributed. Sometimes, technicians put the printed schedule aside and instead look for a Work Order they would rather do. They see the title of the Work Order and think, “I feel like working on that!”
Losing the opportunities of scheduled maintenance work
You might be wondering, “Well, where’s the harm? Why can’t my maintenance workers choose what they want to work on?”
There are several reasons why it’s not ideal – and potentially dangerous – for maintenance workers to prioritize unscheduled work over scheduled work. Here are just some of the reasons why this shouldn’t be the norm at your organization:
- Permits: Work is scheduled when the proper permits have been researched, applied for, and obtained for specific dates. Unscheduled work orders likely do not have the necessary permits to do the work, such as digging or turning power off.
- Tools: No organization has an infinite amount of tools; in fact, some specialty tools might be shared between workers or crews, or may even be rented. Schedulers schedule work when they know the right tools for the job will be available. Unscheduled work has no such guarantee. And without the right tools, the maintenance technician can’t do the job.
- Materials and Parts: Just like tools, a Scheduler ensures that the materials and parts needed to complete the Work Order have been kitted and are ready to go, such as filters, oil, wire, etc. When a maintenance technician decides to tackle an unscheduled Work Order, much of his or her time will be spent gathering parts and materials – or discovering that the parts and materials aren’t available that day. By then, the better part of the shift might be over!
- Equipment: Schedulers will often liaise with the rest of the maintenance Planning and Scheduling team, as well as other departments and crews, not to mention with rental companies and vendors to make sure the right equipment is available, serviced, and ready to be used by maintenance workers at a specific day and time. This could include forklifts, generators, etc. Chances are, this equipment rarely sits idle and is often in use. Which means the odds are high that it will not be available if a maintenance technician discovers they need it while working the unscheduled Work Order.
- Outages: Scheduling an outage takes coordination between several different parties in order to minimize the disruption to people and in some cases, to production. With unscheduled work orders, the outage has not yet been scheduled – meaning that the maintenance technician may arrive at the job site and find that he or she can’t do the work.
- Coordination with people: Different worksites may have occupants that can’t be disturbed or need notice prior to work commencing. In my experience at the Space Center, there were often experiments taking place that could not be interrupted. Not only might this affect the maintenance technician’s ability to do the unscheduled work, but it also can create tensions and conflicts between staff. Schedulers have verified that the right parties have been notified and are prepared for maintenance work – and this professional courtesy helps to foster cooperation with these individuals for future maintenance work too.
- Backup generators: Some work sites require that a backup generator runs while the main power is down – if the work has been properly scheduled, the correct personnel will have the backup generator turned on before maintenance staff get to work. But if the maintenance tech is working on an unscheduled Work Order, he or she might not even be aware that a backup generator is required.
- Temperature control: Depending on the nature of your work, some rooms or areas require specific temperature control to protect machinery, equipment, products, experiments, even artifacts or historical documents. Performing unscheduled maintenance can damage that integrity. If the maintenance gets done at the expense of priceless artifacts, intellectual property or valuable assets, was it really worth it?
- “Man hour” requirements: Schedulers carefully plan the daily and weekly schedules to ensure that enough maintenance technicians are available to do the work – but that planning goes out the window if a maintenance technician goes to work on unscheduled work orders. In that situation, now there may not be enough workers of a particular craft to complete a work order, or not enough hours of availability to complete a Work Order.
- Limited access: In some cases, work sites may not be accessible to maintenance technicians unless the work has been scheduled. They may be closed off or locked, or the maintenance technicians may not have the credentials to enter the site at that day or time, because no one is expecting maintenance work to take place that day. Part of a Scheduler’s job is to ensure that work is scheduled when the site will be open and accessible to the maintenance tech and that he or she has the correct clearance to enter that site and that security is expecting them.
- Preventive maintenance and schedule compliance: Organizations measure schedule compliance to gain insight into how their Preventive Maintenance efforts are faring. They want to see if work starts and finishes as planned, if jobs take longer than predicted (e.g. Job Plans are inaccurate) or to see if there is an excess of emergency work orders (e.g. the maintenance team is stuck in a cycle of reactive maintenance). By tackling an unscheduled Work Order that day instead of a scheduled one, the maintenance worker has just created a Break In – and possibly a Break Out if a scheduled Work Order needs to be moved out of the week – and this affects schedule compliance.
- Regulatory compliance: Planners and Schedulers will have planned and scheduled work to meet certain compliance requirements, such as those set by regulatory bodies like OSHA. These bodies often set specific parameters, such as inspections that must be performed every 30 days. So, while it may seem on the surface like “no big deal” to push today’s tank inspection to later in the week, that decision may in fact push the organization out of compliance.
Most of the reasons lead to one major consequence: wasted time. The maintenance worker spends time preparing for the work order, travelling to the work site, and getting set up, only to find that he or she cannot perform the work.
In other cases, it's the time of the Planners and Schedulers that has been wasted, because they have to do the same work over again.
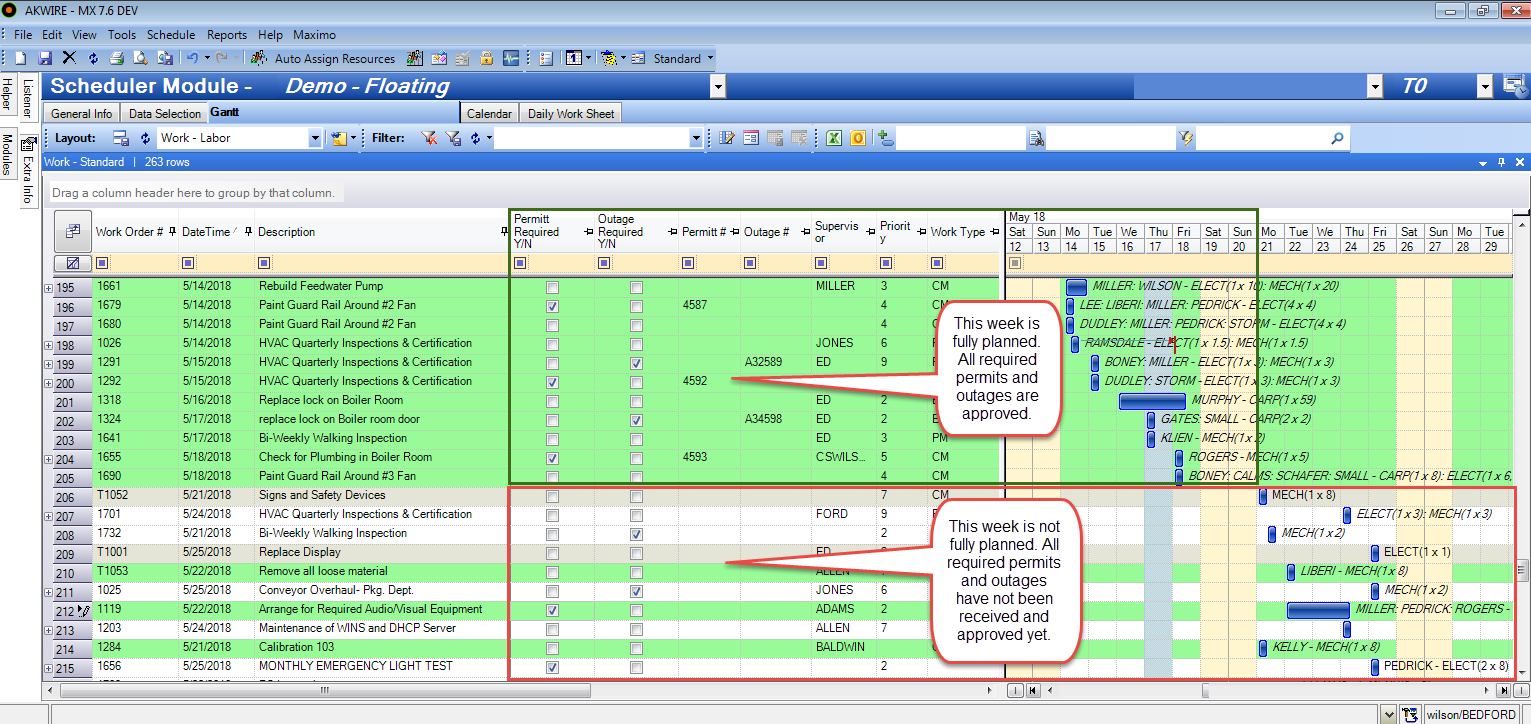
The most important reasons not to work on unscheduled maintenance work orders
While all the reasons I’ve outlined above are important, I want to draw your attention particularly to these three:
- Safety: Unscheduled work orders present a safety hazard for maintenance technicians and others. There’s no ifs, ands, or buts about it. Part of the Planning and coordination process that goes into Scheduling work means doing the due diligence to ensure that it is safe to perform this work – that power is out, the worksite is ready, the right people are informed, the conditions are good, etc. Those precautions have not yet been taken for unscheduled work orders, which means techs who head out to do those jobs could be at greater risk for electrical shock, slipping, equipment problems, etc.
- Re-planning, re-coordinating, and re-scheduling: Of course, some break-in work orders are normal and to be expected. Nobody is ever 100% schedule compliant. But when technicians constantly opt for unscheduled work orders rather than following the schedule, this causes a roll over, like a ripple effect. You’ve got to think, if you’re bringing new work in, other work is getting bumped out. The work that was scheduled for that day now has to be re-coordinated, re-planned, and re-scheduled – essentially, double the work. Those permits the Scheduler requested? They’ve got to get them again. Those planned outages? They need to be rescheduled for another day. This is hugely inefficient – and inefficiency is just another way of saying it damages profitability.
- Wrench time: This is the big one! The goal of Planning and Scheduling is to increase wrench time. Planners and Schedulers coordinate information from various teams and units, combined with the best practices they know to make strategic Planning and Scheduling decisions that lead to optimized schedules. These schedules strive to reduce travel time, work with resource availability, find efficiencies, and capitalize on seasonal opportunities, all with the aim of delivering more wrench time. When workers choose not to follow the schedule, all of that strategic decision-making goes out the window. They might find themselves driving to the same site multiple times a week when they could have driven out there just once. Or perhaps the unscheduled work order leaves only an hour left of availability and there are no one-hour jobs to work on that day.
There’s one thing I can't stress enough: Work is scheduled for a reason.
When work is scheduled for, say, this week, it’s because this week is the right time to do that work. Not next week. Not next month. This week. Schedulers create schedules based on a wide-angle view of the bigger picture: the many needs, priorities, constraints, and roadblocks from numerous sources that dictate how and when work can be done safely, effectively, and efficiently.
It’s their job to understand that big picture and make sure everyone is doing the right work at the right time. A schedule doesn’t exist for a schedule’s sake – it exists to ensure the safety and efficiency of the maintenance team. Encourage your maintenance technicians to follow the schedule wherever possible. After all, it’s not “just” a schedule. It’s the strategic compilation and coordination of information from numerous sources to make the best possible decisions that help the entire organization stay productive and profitable.