Just like no two snowflakes are alike, the same can be said for each person’s career path. Some careers take a long, winding route from their first to their final job, with a few pit stops for life changes thrown in for good measure. Other careers are concise, climbing that workplace ladder in a straight, determined line.
For Jim Martin, his career started with Detroit Edison, now DTE Energy. He has moved from a general laborer to the position of Project Manager Maintenance Improvement. Even though his duties and responsibilities have changed during his tenure, one variable that has remained the same is his employer. Although the average length of employment has gotten shorter for most people these days, Jim is approaching his retirement with the same organization, 43 years after his first hire.
Well before that first job application was filled out, though, Jim knew all about the company through his father. “My dad worked there for just shy of 40 years,” he explained. “I heard stories about it growing up. In a sense, it was always my company.”
Early hands-on training in the energy sector
Jim recalled one time in high school when his father came home from work and Jim was watching the Detroit Tigers on TV. His dad called him out to the car to help him carry in some drawings. Showing him the various diagrams, Jim’s father explained that they were all going to be used to connect the company’s three office buildings together.
“I used to get out of high school,” he said, “and I’d drive there and go on the job site with him. He’d walk me around the site and show me what they were doing and how they were doing it. I could ask the ‘why’s and ‘what if’s and he’d answer those questions.” It was fun, he said, because while he always heard about what his father was doing, he was actually seeing it firsthand.
The sheer magnitude of every process was so much larger than he even comprehended in his experience. Even a simple hole was not just a hole in his father’s world. “They would be digging a hole and it was a huge hole. When you think of digging a hole, you usually think about digging a hole in the back yard. This was much, much larger.”
After high school, he spent his first six years as a laborer for Detroit Edison, which not only served to get his foot in the door and exposure to different trades but it also gave him a very humble perspective. “I was told to do this or do that, a lot of typical cleanup work. We were always picking up after people who would just leave tools around. I made up my mind not to do that to anyone else. I make a point of doing that and it’s something I constantly think about.”
To this day, Jim is conscientious of how his ‘clutter’ might impact people around him.
“One thing my grandmother said when I first went to community college was, ‘Make sure you don’t forget where you came from.’”
Keeping a healthy respect for the power of electricity
Jim’s next move forward with DTE Energy came when he trained to be a journeyman electrician through the company’s internal program. “We had training for one week every couple months. There was a lot of information packed into each week but the more I learned, the more everything seemed to fit in my mind and it cleared up a lot of confusion.”
After the training modules, he was required to go back to work and complete field exercises related to what he had studied in class. The journeymen he was assigned to would ask him to explain something and sometimes even ask him to explain things a different way. “At first, I thought they were being buggers,” he admitted. “But they really helped me.”
Jim recalled being asked if he was afraid of working with the electricity. He was told, “the day you aren’t afraid of electricity is the day you don’t go home. You’ve always got to keep that in the back of your mind.”
As an electrician, he learned to read blueprints “because there are components all over the place.” He also honed his troubleshooting skills. “This gave me the ability to break things down, which is really important.”
Troubleshooting comes in particularly handy when he is working with software and other components, such as. If something doesn’t do what I want it to do, I break it down. You’ve got to make sense of it when you reach out and ask for help.”
While working for DTE Energy, Jim attended the Central Michigan University where he first received a BA in Business Administration, followed by an MSA in Business Administration. “When I was taking classes for my master’s degree, I learned a lot about leadership and how to talk to people.”
His communication skills have been beneficial as he continued to move through different departments and positions at DTE Energy. “The beauty of the job that I have now,” he said, “is that it combines everything I’ve ever done in my career. I’ve done the manual work, the financing, the auditing and the scheduling.”
Choosing the most appropriate tool for the Maximo job
When he accepted his current position as Project Manager Maintenance Improvement, Jim said one of the first things he did was to send an email to all the plant managers to put together a team who can work on IBM Maximo. “I’m blessed that I have the best people in the departments,” he said. “We’ve written procedures, flow charts and process maps. We did all of this before we brought in AKWIRE [Now part of Prometheus Planning & Scheduling].“
Primavera Scheduling Software is powerful, he said, but it’s not suitable for daily work. “It’s like taking a Humvee to the corner store to get a gallon of milk.”
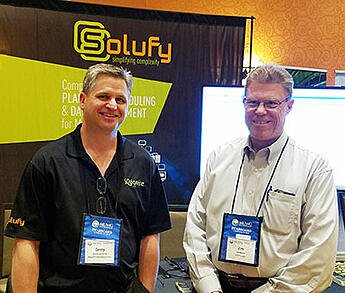
Two years ago, Jim and his team saw an AKWIRE demonstration. After testing other scheduling tools for Maximo, the team circled back to Prometheus. "That looks really good! Can we get that software?” they asked collectively.
Solufy’s Vice President Gerry Lamarche (with Jim in the picture) brought the software in and they started running it through different scenarios. “During the workshop for the Proof of Concept, Gerry was asking his questions so he could configure the software properly,” Jim explained.
“On the second day, prior to lunch, one WMS team member asked me could he start to build a schedule. We asked Gerry and he said that he had enough of the configuration complete. At that point, all seven people in the room were logging into Prometheus in our QA environment and the folks started building schedules without any training.”
Because of its user-friendliness, and because new users had the courage to dive into Prometheus, the first portion of training was far beyond a ‘traditional’ session. “When training started weeks later, the class was not asking how you log in but how do I do this or that.”
Next, Jim and the Work Management Team members from each of the six plants completed training on the software and then went out and trained additional people in their respective power plants. “Now I have a person in every plant who is an expert. If a user has a problem, he calls them first.”
“AKWIRE vScheduler, other than being an excellent scheduling tool, is very intuitive for the end user,” Jim said. “The ease with which it functions between the different modules is part of what makes it so powerful.”
For example, “AKWIRE vScheduler affords the end user the ability to visibly see the backlog in ways that no one else does. It puts so much power into the hands of the folks doing the work, yet makes it so easy to use.”
One person who attended a training was shown a number of open work orders. “They came to me and ask why these are still open, because they were already complete. We just showed them how to change the status of the work orders.” Over lunch, that individual was able to clean up what initially looked like a significant backlog of work orders.
Consequently, Prometheus helps enable an advanced level of operational awareness for the DTE team. That deeper understanding of the software’s capabilities then facilitates even more detailed, helpful interaction with the Prometheus team. “Everybody is very receptive if we have suggestions,” he said. “Solufy [Prometheus] makes it work for you.” This knowledge transfer and building helps the DTE team achieve even more.
As Prometheus continues to help improve functionality across the company, Jim has noticed a definite change in people’s attitudes.
“A couple weeks ago,” he recalled, “we had a training session. One person told me he was there because he was told to be there. ‘But I’m not going to use it,’” Jim was told. “Halfway through the second day, that same person gave me his phone number because he didn’t want to miss anything.
“That is a statement to the tool.”
Recently, Jim received a phone call from a business manager of DTE’s Gas Division. “They want a demo next Wednesday. They’ve heard about it and they want to know how to implement it.”
A representative from the wind/renewable power segment also reached out to him to learn more about Prometheus. “Once people see the tool and what it’s capable of doing, they want to learn more.
“It’s simple to use… but not simplistic,” he was quick to say. “It’s a very powerful tool and it has a lot of great features.”
Encouraging employee-driven innovation to grow the bottom line
Helping to bring Prometheus into DTE Energy was a huge positive for the company, but it was only one of many highlights that Jim has experienced in the organization.
Looking back over the past four-plus decades at DTE Energy, Jim noted a lot of different ways the company promoted employees’ skill sets. For example, they would incentivize employees to suggest innovations to help save the company money. “I loved that,” he recalled. “It made the work all the more fun.”
He credits DTE Energy for listening to these new ideas. Their perspective, Jim said, is ‘If it works, we’ll make it policy; if not, we’ll scrap it.’
In another instance, he was assigned to contribute to a team during a software upgrade. “On the first day, I said, ‘I have no idea why I was put on this project. This is a computer project.’" The IT person he was speaking with responded: "‘I can make the software do a lot of different things, but I have no idea what it needs to do. You need to tell me what you need the software to do and let me figure out how to work it.’ It gave me a whole different perspective,” Jim recalled. “I worked two years on that project and never worked so hard in my life, but I loved every second of it.”
One of the more significant changes he’s seen over the years is the integration of computers into all facets of the workplace.
“Things change a lot quicker now,” he said. “Thirty or 40 years ago, to get a change made, it took an act of Congress. Our culture is more receptive of embracing new ideas now.”
A shift to alternative energy
Another change he sees is the reduction of dependence on coal. “I’ve got mixed feelings about that,” he said. “What the future’s going to be is wide open right now. We know there’s going to be solar; we know there’s going to be wind involved.
“Coal’s going to be history, though. It’s something that is going to be talked about in textbooks. But it is a cost-effective way for making power for people and we can’t just abandon that.” The shift to other methods of power generation needs to be gradual, he said, because if it is done too quickly, “the costs would be phenomenal and your customer gets hurt.”
However, the shift to other power sources are exciting and can benefit even the daily commute. “I’ve had the opportunity to drive an electric car a couple times,” he said. “That was really neat. If I was to continue working, I’d look into buying one.”
Advice from four decades in the energy sector
Four decades has obviously not come without some obstacles or victories. Drawing from his experiences working with DTE Energy, Jim has some short, practical insights to pass on.
“For a person entering this field, I’d say don’t be afraid to get dirty, bring your common sense and pack lots of patience."
“Not everyone will see the world the way you do,” he continued. “That’s ok. Just encourage them to follow along and try explaining that by following good practices you’ll be able to get the right work done and not have to stress out over it.
“And, if you do find yourself in a constant state of stress, you’re not following the correct process.” The processes don’t change, he explained. “The standard in the industry is IPSEC: Identify, Plan, Schedule, Execute, & Close.” But people can alter their understanding of those processes. “The planner looks at a job and decides who and what is needed to get the work done. The scheduler has to get so much work done by a specific date. It’s breaking these components down to the smallest pieces and working with them that way.”
As his career approaches its end, though, he is looking forward to other hobbies, such as woodworking. Jim joked, “The good thing about wood is if what you're building doesn’t work, you can always just throw it in the fireplace.”
He also looks forward to traveling with his wife, who retired a few years ago. “We want to see Hawaii and the Panama Canal,” he said. Sharing a mutual love of history with his wife, he said they look forward to visiting all the areas of the US.
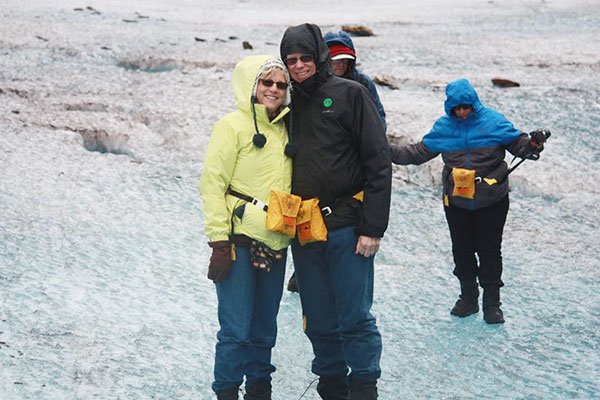
Jim and his wife Barb on Mendel Glacier near Juneau, Alaska.
Regardless of his future plans, the past 80 years combined that Jim and his father worked for DTE Energy will continue to leave a mark on its employees. “A good day for me is working with people and helping to solve their problems. I’ve always wanted to simply make work easier for everybody.”
From a general laborer, through finance and now as a project manager, one purpose has been in the forefront of his mind for 43 years.
“It’s my responsibility to do my job right, and the purpose of our jobs is to get the power out to customers.”
Read the details of how DTE Energy used AKWIRE (now part of Prometheus Planning & Scheduling) to gain new insights and better visibility to bring much-needed consistency across their vast organization.