Forget the partridge in the pear tree or the turtle doves. There’s one gift that stands out above all the rest – and that’s the gift of time. As our one of our colleagues likes to say, “When you have eight hours of availability, that’s all you’ve got. Eight hours. No more, no less. But how you use those eight hours can vary, with dramatically different results.”
Time is of the essence for Maintenance Planners and Schedulers in more ways than one. Obviously, their goals are to ensure that proactive and corrective maintenance work is planned and scheduled in such a way to increase wrench time, ensuring that maintenance workers maximize their productivity during their working hours.
But before they can do that, they have to make those job plans and schedules. And there’s one of two ways to do that work: the slow way or the fast, efficient way. Do skill and experience play a role? Certainly. But the biggest deciding factors that will determine how quickly and efficiently Planners and Schedulers can work are the solutions with which they’re equipped.
So, in the spirit of giving the greatest gift of all, here’s a look at 12 common scenarios that your Maintenance Planners and Schedulers are likely to run into on a regular basis. Do you want them to get these things done as efficiently as possible? Or is it OK if it takes a long time, lots of effort, and may include repeating the same tasks over and over?
12 Days of Planning and Scheduling time savings
On the first day of time savings, I need to…
Assign and reassign resources to Work Orders.
Here’s a common scenario for Maintenance Schedulers: find all the work assigned to a person and reassign it. For example, James works in the Electrical Craft, but he is out sick today. His work needs to be reassigned ASAP.
With the gift of time saving solutions: Planners and Schedulers can deal with short-notice absences on the fly directly in the Gantt. When you update the availability of the tech who is out sick, your heat map will reflect this, therefore creating the visual cue to reassign his work to the next available tech. There are several different fast options to reassign his work from your Gantt.
On the second day of time savings, I need to…
Plan a schedule for the following week without missing any of the latest work.
When planning your schedule, it’s important to know you’re seeing all the current work. But you want to be able to do that without stopping to refresh the data from Maximo and looking to see if any of the new data from the refresh matches the criteria for the schedule you’re currently working on.
With the gift of time saving solutions: With the Listener feature, Maintenance Schedulers never have to worry that they’re working with out-of-date Maximo data. So, you won’t have to waste time constantly refreshing or publishing to avoid this problem. Listener “listens” to Maximo in near real-time. It alerts you when Work Orders have been added or updated that match your schedule criteria -- including new Work Orders that have just come in or changes to existing work that has been edited or updated and is now relevant to your schedule. This way, you can quickly see what Listener has found and decide whether or not to pull the WOs into your schedule.
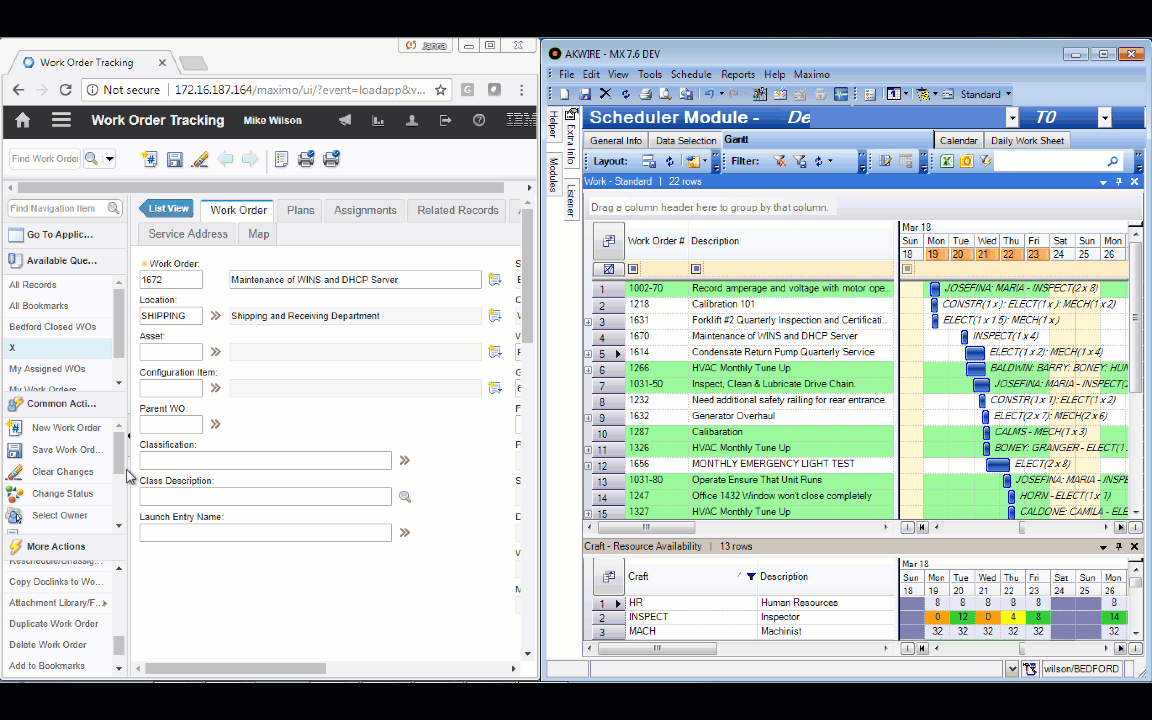
On the third day of time savings, I need to…
Deal with planned availability exceptions, like mandatory training.
As a Maintenance Scheduler, you’ve definitely dealt with situations like this before: for example, remove two hours of availability from the Carpenter Craft for next Monday, because they are all attending mandatory training.
With the gift of time saving solutions: Using our intuitive Calendar module, it’s much faster and easier for Schedulers to enter availability exceptions such as vacation, training, appointments and more. With handy tool bars and hot keys, completing this task is easy-peasy.
On the fourth day of time savings, I need to…
Update dozens of job plans that have a Supervisor who is no longer with organization.
Changes that affect job plans happen all the time. For example, a company might implement new technologies such a mobile CMMS or start using drones to conduct inspections. Or, there may be changes in personnel, compliance, or other protocols. Either way, this can result in dozens upon dozens up job plans that need to be edited.
In other tools, each job plan would need to be manually edited, one at a time. I probably don’t have to tell you that this is so incredibly tedious and time-consuming! There’s simply no reason that Maintenance Planners (given the correct permissions at their organizations) shouldn’t be able to make bulk updates to make the job of keeping their job plans fresh and accurate painless.
With the gift of time saving solutions: While other tools out there don’t have bulk job plan editing and bulk job plan revising, it’s a cornerstone of the Prometheus Routine Maintenance Job Plan module. Why should it take all day to do a task that could be finished in less than a minute?
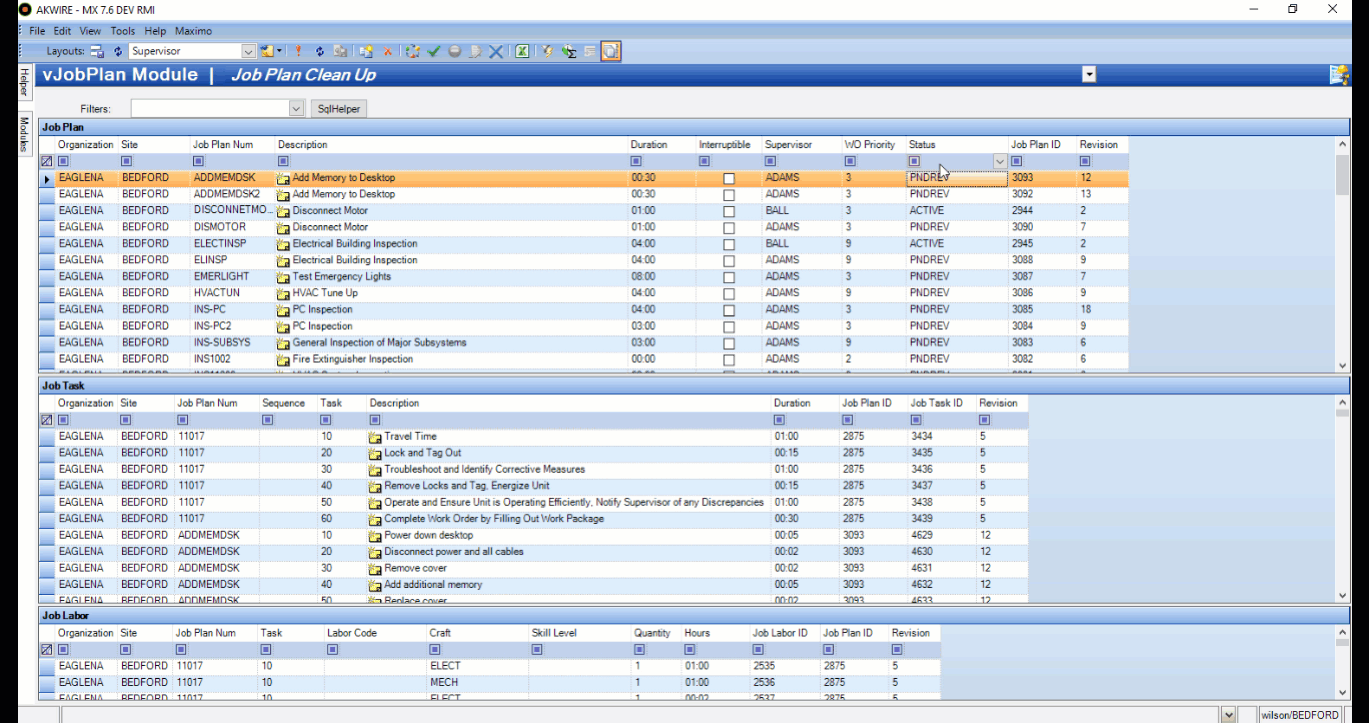
On the fifth day of time savings, I need to…
Monitor compliance when emergency break-in work impacts my schedule.
Every day, Maintenance Planners and Schedulers deal with work that breaks their planned schedules. From bad storms to unplanned outages, break-in work is going to happen. How will you track when break-in work has caused your finalized schedule to change?
With the gift of time saving solutions: There are two ways to track compliance: the easy way and the hard way. The hard way involves a lot of manual work and trying to cobble together a report in your data management/spreadsheet tools. The easy way to is to use the Prometheus Routine Maintenance Compliance feature and let it do the work.
Once your schedule is planned and locked, it will notify you any time work is moved in or moved out of the week that breaks that schedule. And you won’t have to sink hours into building a report. You can easily generate reports that explain what (or who) is breaking your schedule, how frequently, and why.
On the sixth day of time savings, I need to…
Schedule work on an asset that must be brought offline in order to be serviced.
Asset and Location availability is at the heart of Planning and Scheduling. Maintenance Planners and Schedulers can’t do their jobs if they don’t have visibility into which Assets or Locations are ready to be worked on, and which ones are online or operational and can’t undergo maintenance work on those days.
Plus, having this information ensures you can maximize the wrench time of the maintenance technicians by not sending them to job sites or assets that can’t be worked on.
With the gift of time saving solutions: Planners and Schedulers need the ability to see the Asset or Location availability, in conjunction with other vital information such as Work Order, priority, and the constraint or compliance dates.
With Asset or Location overlays, you set the availability in our easy-to-use Prometheus Routine Maintenance Calendar module. It will automatically display this data in color-blocks in your schedule Gantt, so that you can get to scheduling without bouncing back and forth between applications.
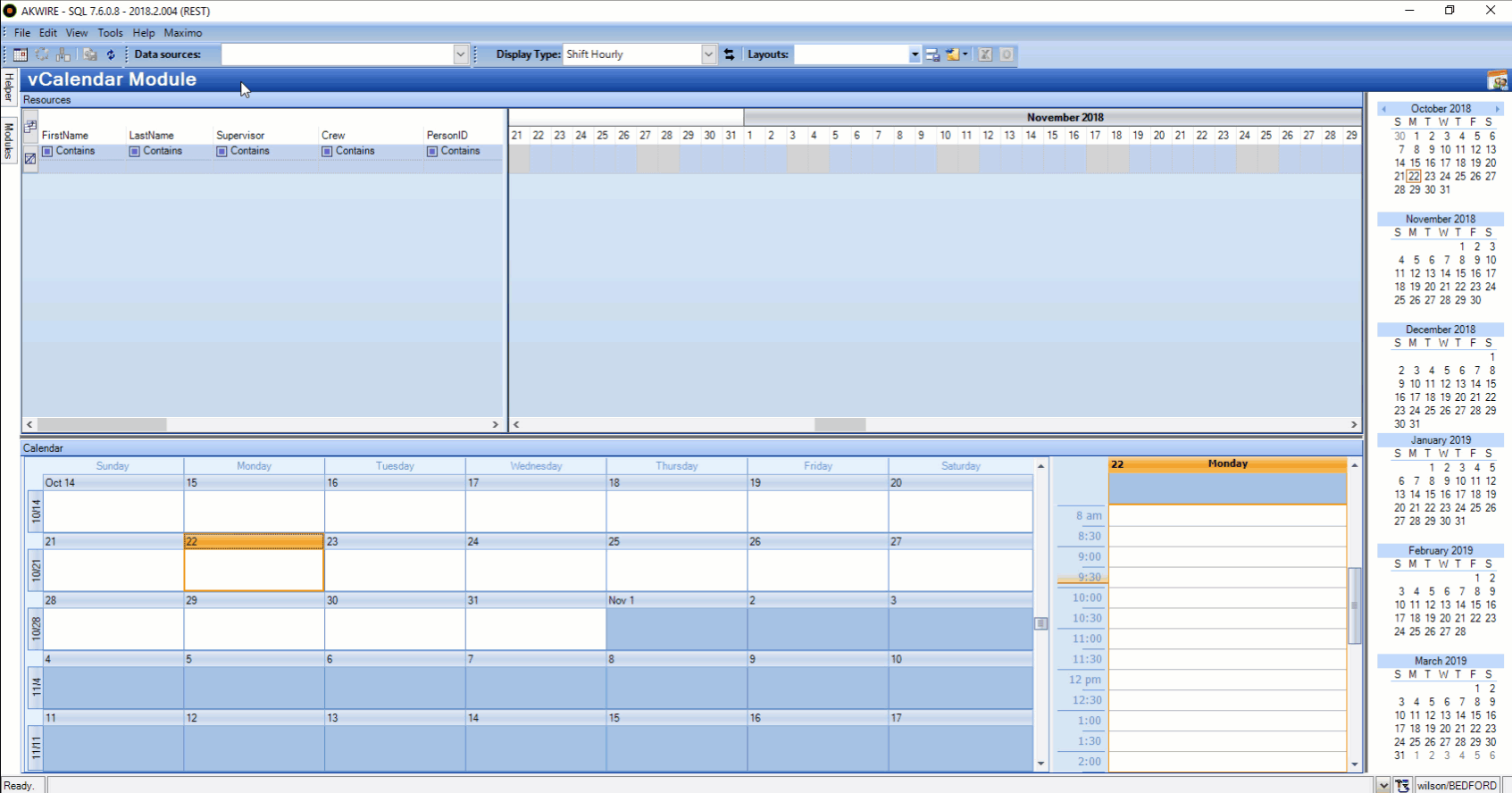
Saving time is the gift that’s on everyone’s mind all year round. And there are just many ways you can save time in Prometheus that we can’t fit it all into one blog post. Find out how Planners and Schedulers everywhere are enjoying the rest of the 12 Days of Time Savings in our next article.